Jaw Crushers are ubiquitous in Quarrying, Mining and Recycling across the world. Their widespread use can be attributed to their ease of use, simple design and powerful mechanical principles to achieve material and rock resizing.
Invented back in 1858 by Eli Whitney Blake patented the Blake Jaw Crusher and is a testament to its sound mechanical engineering as it forms the basis of all modern Jaw Crushers today.
In terms of brute strength and simplicity, the Jaw is unsurpassed and is a common sight in heavy-duty rock and ore crushing.
Today Single Toggle Jaw Crushers have been refined from this 160-year-old design. Using the Keestrack B4 as an example; we can see how modern technologies and design improvements further the field of high production material processing.
A Jaw Crusher uses compression-based crushing to resize material, unlike an Impact Crusher which uses impacts to break up material. In a V configuration, the Jaw Crusher has one Fixed Jaw and one Moveable Jaw. The Moveable Jaw (also known as a Swing Jaw) pivots on an Eccentric Shaft at the top of the Jaw; this has the effect of a 'rocking motion'. The motion carries down the Jaw where it also moves the bottom portion of the Swing Jaw.
Jaw Crushers are simply set by adjusting the C.S.S. (Closed Side Setting), the C.S.S. is the width of the opening during the compressive stroke (the stroke pushing the rock against the fixed Jaw).
The reverse of this is the O.S.S. (Open Side Setting), the O.S.S. is the width of the opening during the open stroke, where the swing jaw is pulling away from the fixed Jaw. This setting is not adjustable; its distance is dependent on the physical size of the Jaw Crusher and Eccentric Throw.
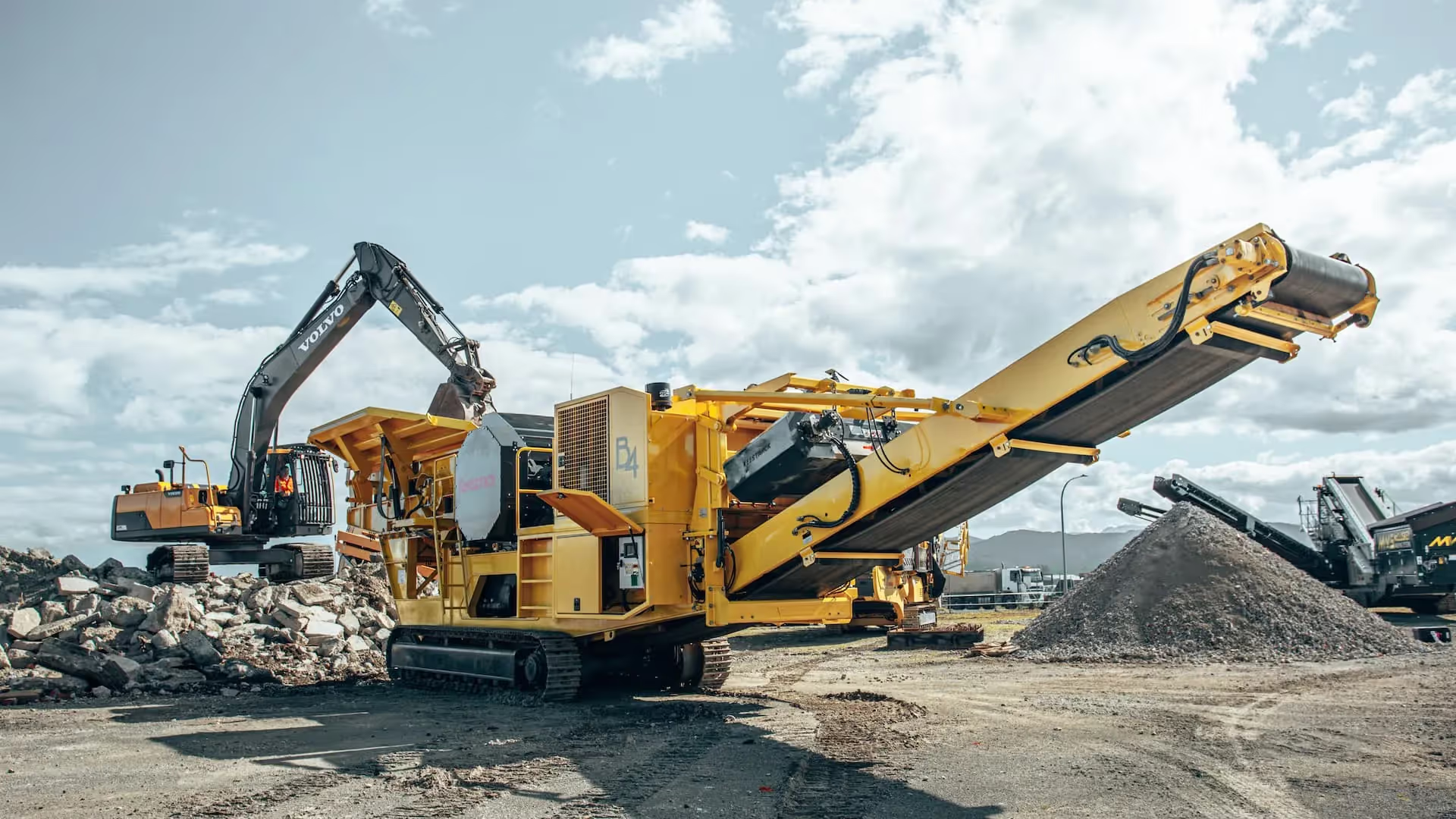
Jaw Crushers reduction ratio is dependent on the actual size of the crushing chamber/box, the larger the opening for feed material, the larger the minimum C.S.S. will be. This is due to the geometry of larger boxes having a larger feed opening, and the feed exit scales up with it.
The Possible C.S.S. range on a Keestrack B4 is 45mm to 160mm. If the C.S.S. is reduced while maintaining a large feed size of 400mm machine load will go up as more energy is needed to complete the Swing Jaws rotation around the Eccentric Shaft.
The ideal Reduction ratio for Keestracks range of Jaw Crushers is 3:1, this is where it is mechanically at its optimum and will produce material efficiently and at a high throughout. At 3:1 it will handle nearly any type of material, particularly hard stone and rock. For medium hardness material the Keestrack range can produce a 5:1 reduction ratio and with soft material like asphalt and lime it can produce an 8:1 reduction ratio.
What separates Keestrack apart from other mobile Jaw Crushers is the extensive development and refinement of the mechanism and introduction of intelligent features that protect the components and reduces possible downtime.
Keestrack implements a full Digital P.L.C. control and monitoring unit on all their crushers, and the Jaw Crusher line is no exception. One of the key benefits is that the P.L.C. will automatically control the feeder to maintain high throughput based on the operators desired input. The P.L.C. monitors and adjusts the Apron Feeder, Jaw Drive and the Non Stop System for high production and in line with the operator set parameters.
One of Keestrack's flagship features if the Non Stop System (N.S.S.) which encompasses a flew slew of hydraulic adjustment and electronic monitoring systems.
- It allows on the fly C.S.S. adjustments while crushing, which means that small adjustments or substantial changes can be done without having to stop the crushing process.
- It incorporates a monitoring sensor which shows the actual C.S.S. of the Jaw to the operator. Whereas most other systems make the operator manually inspect it, to see what it's set and performing too.
- Every 20-50 hours the crusher completes a Jaw reset where the P.L.C. resets the Jaw and C.S.S. according to the wear on the Jaw Plates. The gap setting will always be accurate, regardless of plate wear.
- The systems automatic C.S.S. recovery monitors the set Gap, and if it is pushed back by more than 10mm, the system will attempt to readjust it back to the programmed C.S.S.. If readjustment is unsuccessful and hydraulic pressure on the Gap adjustment rams continues to rise, the system will stop pressurising these rams. Simultaneously the P.L.C. actuates the counter tension ram which pulls the Swing Jaw as far open as possible to dump the uncrushable material.
- The Non Stop System has two overload protections. The first of which is electronic as described above. It also has an instantly operable mechanical relief system. It incorporates 600 Bar pressure relief valves on the cylinders. Should an uncrushable piece of material enter the chamber before the electronic system can adjust for it; the mechanical system prevents damage to the crushing chamber and importantly, their components. Both of these systems also stop the Feeder and Eccentric drive, stopping material pile up.
- Lastly, the Gap adjustment cylinders can be manually operated to crush material that is blocking regular crushing action. This prevents the need for someone to manually unblock the crusher, making it safer and reducing potential downtime.
The Keestrack line of Jaw Crushers are true mobile quarrying and processing machines, highly capable and designed for performance. They save companies money.
How the Keestrack range of Jaw Crushers achieve a more profitable product:
Less Fuel Usage
Keestrack's Jaw Crusher range feature Load Sensing Pumps that distribute hydraulic power to components accordingly. This feature doesn't restrict hydraulic flow; rather, it directs the pumps to generate and direct hydraulic power when it's needed. This system saves companies around 20-25% in fuel costs, which can add up to around $10,000 a year.
Automation
Sensors located throughout the machine monitor load, fill levels and capacity. The P.L.C. can report on what the Jaw Crusher is doing at any moment in addition to working in the set range, keeping the crusher running efficiently and at capacity.
Smart Features
The smart features add to the Jaw Crushers productivity. The wireless remote enables total machine adjustment and even tracking while crushing.